Introduction
This document contains the specifications set forth for all Printed Circuit Assemblies (PCA) and Printed Circuit Boards (PCB) that are handled by IMSAR, LLC or its subcontractors or suppliers. This document contains allowable PCA/PCB handling, storage, and shipping standards applicable to IMSAR’s suppliers.
It is the responsibility of the subcontractor or supplier to meet all requirements expressed in the purchase order, fabrication drawings, applicable IPC standards, fabrication instructions (such as “readme” files), and this document unless specific written permission for deviation is issued by IMSAR, LLC.
Materials
All printed circuit assembly treatments will adhere to the materials specified in the master drawing.
Handling
To prevent Electro-Static Discharge (ESD) and Electrical Over Stress (EOS) damage to sensitive components all handling, unpacking, assembly and testing shall be performed at a static-controlled workstation.
Suppliers shall ensure PCAs/PCBs are protected from environmental, handling and storage damage. Suppliers should have documented procedures that outline these preventative practices. Quality system specifications ISO 9001 and SAE AS9100 require these procedures. Suppliers shall reference IPC-A-610, Chapter 3 Handling Electronic Assemblies to meet this requirement.
It is paramount that untreated/uncoated silver immersion finished PCAs/PCBs not be handled with bare skin contact.
X-Out Policy
IMSAR, LLC will allow for the receipt of X-Outs on PCB panels with the following conditions:
- Each panel will contain no more than “N” number of X-Outs of PCBs per panel.
PCBs Per Panel | Allowable X-Outs |
2 | 0 |
3-5 | 1 |
6-10 | 3 |
11-20 | 4 |
Table 4-1: X-Out Table
- Each X-Out board shall be marked in a manner so as to make the X-Out obvious. Marking shall be indelible and applied to both sides.
General Requirements:
Documentation
- Include a Certificate of Conformance (C of C) that includes information about the treatment type with each order. For example, a conformal coat treatment should include at least coating material type, measured thickness, and measured tolerance. Also included are a serialization sheet detailing the serial numbers for all parts in the delivery, and any other test results required by the drawing or purchase order. If test reports were supplied with a previous delivery, it shall be noted in the C of C.
- For PCBs using Rogers RO4450B Prepreg or RO4450F Prepreg, include a report documenting the pressure applied to parts during the lamination cycle.
Packaging
To help ensure board performance for PCAs/PCBs, IMSAR, LLC requires that suppliers follow the guidelines set forth below for the storage and packaging environments of PCBs.
- Unless otherwise specified in the drawing, printed circuit boards shall be packed in static shielding packaging. a. Silver Immersion finished PCAs/PCBs which are not treated or coated shall be packaged as described in Section 2 below.
- External packaging shall protect the PCAs/PCBs from shock and physical damage, and prevent movement during shipping and handling. Sealed bags containing PCAs/PCBs shall be wrapped in anti-static foam, bubble wrap, or other suitable static dissipative cushioning material. External packing shall also resist tears, puncture opening of seams or corners, and other breakdowns.
Silver Immersion Requirements – Untreated
Documentation
- Include a Certificate of Conformance (C of C) with each order, a serialization sheet detailing the serial numbers for all parts in the delivery, and any other test results required by the drawing or purchase order. If test reports were supplied with a previous delivery, it shall be noted in the C of C.
- For PCBs using Rogers RO4450B Prepreg or RO4450F Prepreg, include a report documenting the pressure applied to parts during the lamination cycle.
Packaging
To help ensure board performance at the coating stages for silver immersion finished PCAs/PCBs, IMSAR, LLC requires that vendors follow the guidelines set forth below for untreated/uncoated PCAs/PCBs:
- Prior to packaging, ridged and flexible PCAs/PCBs shall be clean and dry.
- Silver immersion PCAs/PCBs shall be packaged in a moisture barrier bag (MBB) with desiccant, a humidity indicator card (HIC) and a corrosion control absorber patch (e.g. Silver Saver® paper). Desiccant shall be sulfur-free Type II per MIL-D3464, with quantity IAW IPC/JEDEC J-STD-033. The MBB shall have a water vapor transmission rate (WVTR), as received, of 0.002 gm/100 in2 /24 hrs or less IAW IPC/JDEC J-STD-033. One sheet of Silver Saver® paper (minimum 2.0 x 3.5 in) shall be included for every 140 in2 of bag area (counting both sides). For printed boards with immersion silver finish, a sheet of Silver Saver® paper shall cover each silver surface.
- Desiccant packs, HICs, Silver Saver® paper patches, and Silver Saver® paper shall be kept dry before being sealed in MBBs, and removed from dry storage and placed into the MBB just before it is sealed. The desiccant and Silver Saver® paper shall be kept separate from the product by either of the following means:
- Place the desiccant packs and Silver Saver® paper strips into a secondary small polyethylene bag as shown in Figure 5-1, which shall then be placed in the MBB. The polyethylene bag shall be partially heat-sealed to prevent the contents from shifting, but a gap must be left to allow air exchange to the inside of the polyethylene bag.
- Place the desiccant and Silver Saver® paper in the bottom of the MBB, leaving room at the top for the printed board and HIC. Make a partial heat-sealed seam separating the desiccant and HIC from the printed board approximately as shown in Figure 5-1.
- The MBB shall be heat sealed at the top with light air evacuation; full vacuum is not allowed. The heat seal shall allow sufficient space for the bag to be cut open and resealed at least once. Examine the primary heat seal and verify that there is an uninterrupted dull gray line across the full width of the bag, with no folds, melting, or shriveling. A watery clear glaze indicates that heat has not sufficiently penetrated the bag film.
- Flexible printed circuits shall be supported with sulfur and chlorine-free cardstock or other stiff material to prevent damage in shipping.
- PCAs shall not be packaged in bulk quantities in excess of 1 per MBB, while PCBs shall not be packaged in excess of 10 per MBB.
- Each MBB shall be labeled with the supplier’s CAGE Code, purchase order number, and the part number, serial number, and date code of each part enclosed.
- Finished rigid and flexible printed boards supplied to this order that have been left out of dry storage for more than 5 days shall be baked for moisture removal prior to packing IAW IPC-1601A. Within one hour after any baking, parts shall be stored at less than 10% RH, or dry packed in a MBB as described herein.
- External packaging shall protect the printed boards from shock and physical damage, and prevent movement during shipping and handling. Sealed bags containing PCAs/PCBs shall be wrapped in anti-static foam, bubble wrap, or other suitable static dissipative cushioning material. External packing shall resist tears, punctures, opening of seams or corners, or other breakdown.
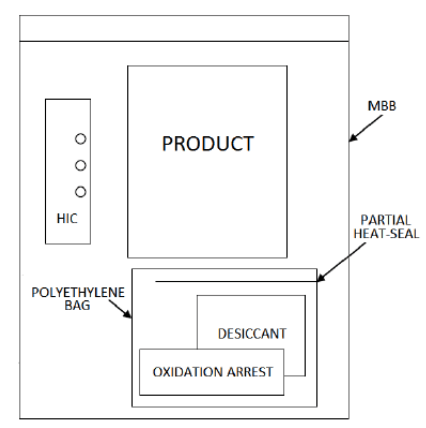
Figure 5-1: Usage of Heat Sealed Polyethylene Bag in Conjunction with MBB